Can A Shared Biomanufacturing Facility Be The Answer To The Demand Forecasting Dilemma?
By David Radspinner, et al
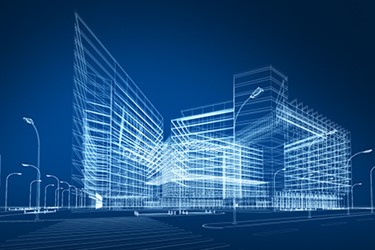
Looking across the landscape of the biopharmaceutical industry, there is more promise than ever to effectively serve global healthcare needs. In 2017, the FDA approved five biosimilar products, paving the way for “follow-on biologics” to be a key factor in global market growth over the next 10 to 15 years.1 Other promising advancements, such as the development of cancer immunotherapies Keytruda™ and Opdivo™ and the rise in antibody drug conjugates (ADCs) and gene and CAR T-cell therapies, show the growing pace of therapeutic and molecular innovation. The refined understanding of disease biology that has led to these exciting developments is driving the industry to target smaller patient populations, meaning the growing number of biologic drugs coming down the pipeline, especially when combined with improved potency of therapies, will be manufactured in smaller volumes.
Not only does this increase the need for more flexible and efficient manufacturing, but it also intensifies the spotlight on the long-standing problem of managing demand uncertainty in biologics production. Traditional stainless-steel facilities can take four to six years to build, which requires construction to begin several years before you even know if your product will be approved, let alone be successful. If you end up underestimating demand, you must, as quickly as possible, procure additional capacity. In the meantime, you are creating a drug shortage for patients in need of treatment. If you overestimate demand, you end up with unused capacity.
Get unlimited access to:
Enter your credentials below to log in. Not yet a member of Life Science Leader? Subscribe today.